Sheet metal cutting and bending are crucial processes in many industries, including manufacturing, automotive, and construction. Understanding how to properly cut and bend sheet metal is essential for creating strong, precise components. Whether you're working on a small-scale DIY project or large industrial tasks, mastering these techniques ensures high-quality results and reduces waste. Here’s a guide to help you navigate the process effectively.
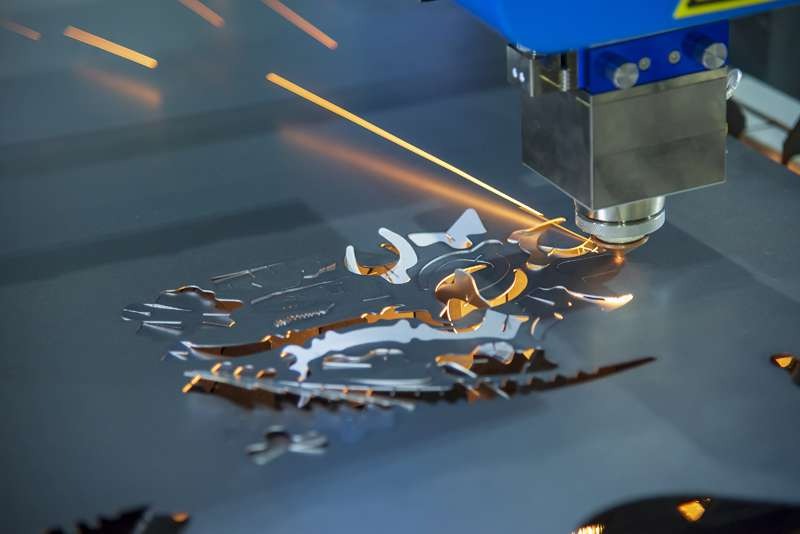
1. Cutting Sheet Metal: Techniques and Tools
The first step in many metalworking projects is cutting the material to the desired shape and size. There are several methods available, each suited for different types of metal and desired outcomes:
-
Shearing: Shearing is the process of using a tool to cut sheet metal along a straight line. Mechanical shears or power-operated machines are commonly used for this purpose. This technique is ideal for cutting relatively thin sheets of metal quickly and efficiently.
-
Laser Cutting: For high-precision cuts, especially in thin or intricate designs, laser cutting is a top choice. Laser cutters provide a clean edge with minimal distortion and are highly effective for detailed patterns. However, this method requires access to advanced equipment and can be more expensive.
-
Plasma Cutting: Plasma cutters are commonly used for thicker metals and produce a highly accurate, clean cut. While they generate more heat than laser cutters, they can handle a wider range of material types and thicknesses.
-
Nibbling: Nibbling involves using a punch and die set to remove small sections from the sheet metal. This method is ideal for smaller cuts and shapes but is generally slower than other cutting methods.
-
Manual Tools: For smaller projects or when you don’t have access to heavy equipment, manual tools like tin snips or aviation shears can be used to cut sheet metal. These are affordable and easy to handle, though they may be less precise compared to powered methods.
2. Bending Sheet Metal: Techniques for Precision
Once the metal is cut, the next step is often bending the material to create specific shapes or angles. The most commonly used methods for bending sheet metal include:
-
Brake Press Bending: A brake press uses a powerful mechanical or hydraulic system to bend sheet metal. This process is highly accurate and commonly used for creating V-shaped or U-shaped bends. Brake presses can be adjusted to different angles, making them versatile for various applications.
-
Air Bending: Air bending involves pressing the sheet metal against a die and punch to create a bend at a specific angle. Unlike bottom bending, the metal doesn’t have to conform exactly to the shape of the die, which allows for more flexibility in the types of bends you can make.
-
Bottom Bending: In this method, the metal is fully pressed into the die, creating a precise bend. Bottom bending is ideal for producing sharp, accurate bends but requires more pressure than air bending.
-
Roll Bending: For creating curves or cylinders, roll bending is the go-to method. This involves passing the sheet metal through a set of rollers, gradually forming the desired curve.
-
Hand Bending: For simple bends, or when working with thinner sheet metal, hand bending tools like a manual bending brake or a clamp and hammer can be used. This technique requires good control but is effective for small projects.
3. Key Considerations for Successful Cutting and Bending
To achieve the best results when cutting and bending sheet metal, consider the following factors:
-
Material Thickness: Different tools and techniques are suited for different thicknesses of sheet metal. Always choose the appropriate equipment based on the material you’re working with to ensure a clean and accurate result.
-
Angle Accuracy: Especially when bending, precision is key. Ensure your measurements and equipment settings are accurate to avoid distortion or misalignment.
-
Tool Calibration: Whether you’re using a manual tool or a powered machine, always check that your equipment is properly calibrated. This ensures consistent results and reduces the risk of errors.
-
Safety Measures: Working with metal can be dangerous due to sharp edges, high heat, and heavy machinery. Always wear protective gear such as gloves, goggles, and ear protection. Additionally, ensure your workspace is clear of debris to avoid accidents.
-
Practice and Patience: Mastering metal cutting and bending requires practice. Take your time to experiment with different materials, tools, and techniques until you find the approach that works best for you.
4. Conclusion
Mastering the techniques of cutting and bending sheet metal is essential for achieving high-quality, precise results in any metalworking project. Whether you’re a professional metalworker or a hobbyist, understanding the different methods and tools available will help you streamline your processes and achieve the desired outcomes. By choosing the right equipment, paying attention to safety, and practicing your skills, you’ll be able to handle a wide range of metalworking tasks with ease and confidence.